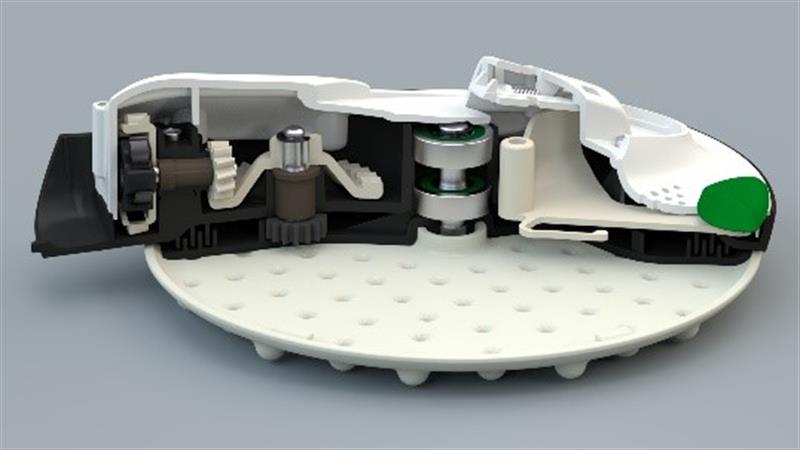
This innovative household appliance module with 29 individual components was created by Lüttgens in close cooperation with the customer in a project with several development and test phases. The automated assembly line for the modules, also supplied by Lüttgens, incorporates real-time functional checks and QC testing of the subassembly groups processed.
Heiligenhaus / Germany, April 2018 – At the HMI trade fair Lüttgens Kunststoff-Technik
will showcase its know-how as a powerful partnerfor complex assemblies used in wide-ranging applications.
Customers profit from Lüttgens' in-depth expertise and close cooperation in design and development of multi-component modules. Maintaining an open dialogue in every stage of the project, Lüttgens develops and implements all-inclusive solutions for manufacturing of individual components with automated fabrication and testing in the subsequent assembly process. Their decades of specialised experience and know-how in the hybrid component sector offer particular benefits in projects of this kind. The Lüttgens engineering team are experts at realising and integrating multiple functions in components with different materials of construction. The results – fewer individual components, simplified assembly and therefore upgradedproduct reliability – speak for themselves.
Masters of their craft, Lüttgens' engineers provide solutions for technologically demanding fabrication processes with high automation levels and short cycle times as required for efficient series production with hybrid components. Their wide-ranging experience – in this area as well as in the fields of multi-component and gas-assisted injection moulding (GIT) – offers big advantages to manufacturers of a broad variety of products including automotive components, sanitary systems, household appliances, electric construction components and systems and mechanical engineering.
Plastic/metal hybrid technology is a sector with great future potential which creates new paths for weight-saving construction.Synergistic effects between the properties of plastics, metals and other materials of construction provide unlimited design options for compact, lightweight and cost-efficient hybrid components tailored to the specific application at hand.
Lüttgens offers lightweight hybrid solutions, co-injected systems with high functional integration and composite mouldings with superb rigidity and toughness, all in great demand in the automotive sector. The company has achieved industry-wide recognition as an expert supplier of outer door handles, suspension components and gear sticks and now ranks among Europe's leading providers of overmoulded lock components. Continuously refining the automation level and networking of manufacturing equipment and machinery in their plants in Germany and Poland, Lüttgens meets and exceeds customers' requirements with cost-efficient and environment-friendly series production.
Lüttgens, a family-owned company under third-generation leadership, has production operations in Heiligenhaus/Germany and Kurzętnik/Poland with an overall workforce of 310 employees. The company manufactures technical
injection mouldings and assemblies made from advanced engineering plastics to exacting specifications. Offering benefits from decades of development and production experience as well as close contacts with materials manufacturers,OEM and systems providers, software developers and universities worldwide, the Lüttgens know-how portfolio is customers' assurance of substantial time savings and outstanding cost efficiency.